In order to seek perfection, intentional systems and safety must both exist, and when they do, that’s when you’ll be exceptionally well-positioned for world-class success, and that’s when you truly unleash the potential of your team, which then allows your team to learn their way toward perfection.
“Seek Perfection,” one of the Shingo Guiding Principles (in the Continuous Improvement dimension of the Shingo Model), may seem to imply something we imperfect humans cannot achieve. Bill Boyd, Value Capture Senior Advisor, dove into this principle in a Shingo webinar he presented, “Learning Your Way to Perfection.”
Bill begins by sharing the Shingo definition of perfection:
Perfection is an aspiration not likely to be achieved, but the pursuit of which creates a mindset and culture of continuous improvement. The realization of what is possible is only limited by the paradigms through which we see and understand the world.
Bill highlights these words from the definition – Aspiration; Pursuit; Mindset; Culture; and, Paradigm – to begin to turn these somewhat theoretical-sounding words into tangible, actionable realities. He does this first by sharing experiences he learned from his time as an operational leader in a health system several years ago. When he managed lab operations, and guided by the enterprise goal of providing perfect patient care at the lowest possible cost, Bill describes how he and his team first mapped current processes. They came to realize the better way (more rapid, impactful and sustainable) to improve was to challenge their paradigms and embrace the mindset of “what does it mean to deliver a perfect laboratory service?”
What would be the most ideal way to meet that need [perfect laboratory service] free of barriers inherent to the work as it had been designed? What’s the most perfect way to complete our work, step by step, meeting the need?
Why Can’t We…?
As they freed themselves from their paradigm, Bill and his team began to create a new paradigm, embedding the mindset of seeking perfection. They framed their thinking about their work and improving their work through this question – Why can’t we…?”
Through this lens, obstacles to improvement became clear, making it easier to hypothesize potential solutions, experiment and test hypotheses, measure, adjust, rapidly learn and rapidly improve. In other words, Bill and his team began to rigorously and continually “learn their way toward perfect.”
Theoretical-Limit Thinking
Through years of study (including the work of Paul O’Neill, Sr.) and experience, Bill has expanded the frame of “why can’t we” to the frame of theoretical-limit thinking, defined as:
“Where aspirational goals should be set, at perfect or as close to perfect as the rules of physics allow.”
This mindset gives permission to, and fully enables everyone to envision what perfect would look like, and opens wide the door to thinking about experiments to implement to bring that vision to life.
A Required Element of “Seeking” –Intentional Behaviors
With the understanding of what perfection is and a frame to envision perfect, Bill moved the discussion to “seek,” the verb in the Shingo principle of Seek Perfection. He notes that “approaching improvement in a structured way” is a behavioral benchmark of the Seek Perfection principle, and that scientific-method thinking is the structured way toward improvement. PDCA (Plan-Do-Check-Act (or Adjust) is the model for scientific-method thinking. The structure requires that we first grasp the situation by understanding the current condition, to identify the problem. We then create a hypothesis, our plan, to solve the problem (if we do x, then y should be our outcome). We implement our action plan (“do”), with specific steps to achieve our expected outcomes and establish metrics to let us know if we achieve our target. “Check” is our next step, in which we objectively assess what our plan achieved per our target metric. This requires evidence-based, show-the-data method, which allows for objective analysis and understanding. With the data in hand, the team can identify gaps, and begin to Act/Adjust, with hypotheses about how to close gaps, design experiments to close gaps, and begin the PDCA anew.
It is this structure of PDCA that allows us to learn, improve, and “seek perfection” through taking action and doing. Bill discusses the close relationship between the Guiding Principles of “Seek Perfection” and “Embrace Scientific Thinking” (also in the Continuous Improvement dimension). Critical to understanding whether principles are embraced and lived, or not, Bill identifies behaviors that demonstrate Embrace Scientific Thinking. These include:
- My organization supports everyone’s active involvement in using problem solving systems in our daily work.
- My team carefully collects and analyzes good data and facts to determine whether evidence supports a proposed improvement or innovation.
- My team actively engages those closest to the problem in all phases of problem solving and process innovation.
Another way to think about this is, to seek perfection requires the existence of a robust learning culture throughout the organization.
Another Required Element of “Seeking” – Safety
Understanding “perfection” is part of the equation, but the freedom to think about perfect is not the same as the freedom to call out and talk about problems to begin the process of solving problems. There must be “Safety” throughout the organization so frontline workers and supervisors, and managers and leaders of all levels can, without fear of repercussion, call out problems, harm and risks of harm. (Value Capture refers to this as “psychological safety”). Bill describes some behaviors that would demonstrate the level of safety needed to empower and encourage call-outs. These include:
- Team members offer novel ideas freely.
- Team members seek additional information and understanding about their colleagues’ ideas.
- Team members speak freely, even if their opinion is different from others.
- Team members look you in the eye when sharing their thoughts.
Bill concluded the presentation by saying, “Without safe behaviors throughout an organization, improvement will be tempered. Without an intentionally designed system that drives learning behaviors, improvement will be sporadic and episodic. And without safety, improvement will be limited as a result.”
You can watch Bill’s webinar here, and you can read Bill’s blog posts, Seek Perfection – A Shingo Guiding Principle for Continuous Improvement, here, and Don’t Let Your Knowledge Threshold Hold You Back, here. To learn more about how Value Capture might help you create a learning culture and learn your way to perfection, please complete our Contact Form.
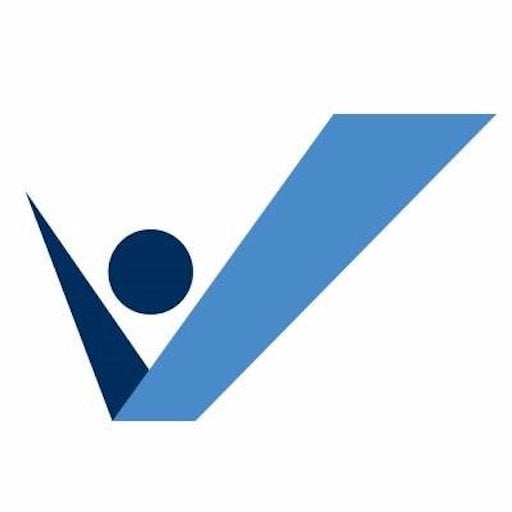
Written by Value Capture
Value Capture supports chief executives who seek to transform the performance of their healthcare organization in safety, quality and profitability.
Submit a comment