In 2019, Meghan Scanlon (a former Value Capture advisor) presented a webinar, “Pursuing Zero Harm: A Powerful Platform for Embedding Lean Capability.”
Value Capture Senior Advisor Mark Graban moderated this webinar (hosted by our partners at KaiNexus).
In this webinar, Meghan laid out the importance and impact on performance excellence that the goal of zero harm has, the underlying principles, real-time problem solving and “everyone, every day,” and the role of the leaders in setting aspirational goals and providing the support and systems necessary to enable the workforce to continually improve toward perfect.
This post shares some of the highlights from this webinar, which can be viewed below:
Learning Objectives, Principles, and the Power of Zero Harm
Meghan set forth three objectives of this webinar:
- Learn the power of a zero harm goal to accelerate improvement
- Understand the importance of safety as an organizational value and how to use it to engage people in improving their work
- Learn how a focus on safety can be used to embed Lean capability
Noting that Value Capture’s work is focused on the healthcare industry, Meghan added that she hoped “to not just focus on healthcare itself, but to really transcend that industry and to…
"…Get to the universality of some of these concepts and values and principles that, when applied in your organization with proper focus and leadership behaviors, can accelerate and drive an organization’s ability to transform and improve operationally for sustainable success."
Meghan briefly described Value Capture’s partnership with the Shingo Institute, as a Shingo Licensed Affiliate.
“The importance for me and my belief in the Shingo Model is the connection between principles and behaviors. Infusing and having a value focus in an organization and understanding how systems, tools, results lead to the culture and behavior of an organization can be critical to think about as you start to plan your transformation strategy.
One of the key things that I take away when thinking about this Model and what it can mean to your organization and leadership is the idea that the systems that exist in any organization are perfectly designed to get the results that you are getting. So focusing on what opportunities or problems exist in organizations should lead, always, to the improvement of those systems and understanding how the processes affect those systems. This idea that we can design ideal behaviors into a system that connects tightly to values and principles is one that I think is really important, as we begin to think about our transformation journey.”
The Three Questions of Paul O’Neill
Meghan discussed values by talking about Paul O’Neill’s three questions. O’Neill said that organizations have the potential to be habitually excellent when everyone in that organization could answer “yes” every day to three questions. These are:
- Am I treated with dignity and respect by everyone I encounter, without regard to race, gender, educational attainment, rank, or any other distinguishing characteristic?
- Am I given the tools, training, resources and encouragement I need to make a contribution to the organization that adds meaning to my life?
- Am I recognized for that contribution by someone whose opinion matters to me?
“I encourage you to think about these three questions and how you would answer them. How would your staff answer them? How would the leaders in your organization answer them?”
The Power of Zero Harm and Seeking Perfect Performance
Meghan briefly reviewed the performance of Alcoa during (and after) the tenure of Paul O’Neill as CEO. From day one of his tenure, O’Neill set forth the goal of having zero worker injuries. Although some may think setting such a goal could be demoralizing (since humans are fallible), O’Neill’s vision and unrelenting advocacy for zero harm unleashed wave after wave of innovations, a wholly engaged workforce, and incredible financial performance.
“The idea of using ‘zero’ as a platform and as a goal, so that you can have sustainable, long-term change that can withstand leadership changes, can withstand the test of time, can really be something that, even after leaders move in and out of organizations - it gives you that focus that you need. Zero is attainable and possible.”
Across more than 300 worksites around the world, Alcoa continually worked to improve toward zero harm, achieving zero lost workdays at 82% of its sites.
“Were they perfect? No. Was the journey yielding what they expected? Were they instilling and infusing the right values into the organization with principled leadership, and embedding understanding how to systematically reduce harm, to improve processes, and the management principles and the behaviors needed to sustain long-term change? Absolutely.”
The Value Capture Approach, and a Challenge
Meghan gave a brief overview of the Value Capture approach to transformation. “Value Capture’s approach follows the scientific method, or PDSA. We first want to understand and assess the current state, and understand the needs. Then, aligning around True North goals, with all leadership levels setting that vision and strategy forward. And then, it’s about how we do three basic things:
- How do we enable ourselves to call out and solve problems, every day, to root, in real time?
- How do we then use the information we get from the real-time problem solving to systematically redesign and improve our value streams or pathways?
- What are the management system needs that exist that we need to develop in our organization to sustain and prioritize these changes?
"The goal at the core of all of this work is to develop people, transform the work, and improve and spread.
I think how we use this [approach] and infuse the safety focus into it is something that can really accelerate and engage and empower an organization towards rapid improvement, sustainably."
"So here’s the challenge. What if no one ever fell? What if no one ever acquired an infection in our care? What if no one ever injured their back moving anyone or anything? What if no one ever got hurt at work?
What would need to be true in your organization for this to be a reality? What leadership behaviors, what processes, what problem solving? What level of engagement from leaders, staff, stakeholders? There’s a role for everyone in a true organizational change like this."
"Keeping that challenge in mind, that any harm is a problem, and problems are gifts, and problems are meant to be solved and learned from, is key to how you rally an organization towards improvement.”
Why Zero?
For Meghan, zero harm is so important because of the idea of a True North goal, “versus an operational or incremental target. The idea behind ‘why zero’ is, if we think about how our current systems are perfectly designed and capable of producing the results we get, the idea that, to truly get to zero, to truly get to perfect, to truly eliminate harm, will require us to think completely differently than we do right now."
"So often, when we set incremental goals, we can get bound by the constraints that exist in our systems. Setting a target as aspirational as zero can really force us to think outside the box, to realize that we need to completely tear down everything that exists today, to really forget about life as we know it, and to really look towards what is it that we have to drastically change in order to get there."
"It gives us a measurable goal, also. Safety, while it can be thought of as a quality metric, it’s also very quantitative. Having a goal and a focus of zero harm gives us a very tangible way to [measure performance]."
Why Safety?
Change management is vital to the success of transformation and improvement initiatives in general. “A big thing with change management is understanding the ‘why’ of something is happening. A key piece of this is, how do we tap into and win the hearts and minds of our organization? It’s got to be something that speaks to them, it’s got to be something that is universally applicable to all of us. That can be a really difficult thing to find….
"What’s something that unifies all of us in our work? It’s the people who are doing the work, and people don’t want to be harmed at work. So using safety as a value is something that is relatable and universal to all of us.”
Meghan also noted that safety is measurable and unassailable, a value that everyone instinctively aligns with - safety is unarguable.
Everyone, Every Day to Solve and Prevent Harm Incidents
“Everyone, every day, is another key to long-term organizational change.” Meghan said that leaders of all levels typically are the “rockstars” of solving problems (perhaps even experiencing promotions due to their problem-solving ability). There are, however, only so many leaders in an organization, and too many problems and challenges."
“If we can expand and think about what it would take or how many problems we could solve to include everyone and improve everyone’s ability to solve problems, think about the potential and how many problems we could solve. Think how much better we could get every single day if we were able to leverage the power of every single person in the organization towards improvement."
"It also hits on the idea of, how do we live respect, what does respect look like? And this idea that the people who are most equipped to solve problems are the people who are actually doing the work. So a big way to show respect is to include the people who are doing the work in the problem solving.
That will help to accelerate the amount of improvement you can have because of the number of people you have focused on it, and to change the leader’s role a little bit into more developmental and coaching as we work to develop the capability of the organization to solve problems."
Four Capabilities to Become a Problem-Solving, Problem-Preventing Organization
Hopefully, there aren’t many harm events in organizations to react to, so attention should also turn to becoming proactive to prevent harm.
“Really thinking about how we can be more proactive in our problem solving, and share what we learn from those events that do happen can help, because not everyone should have to experience the same harm in order to prevent that harm from happening elsewhere.”
“When we think about [incident prevention], and what it takes to embed Lean into our organization in order to have that long-term, sustainable improvement, we talk about four different capabilities from Steven Spear’s High Velocity Edge.”
The first capability is to be able to see problems as they occur. The second is to “swarm and solve” problems as they are seen. Third is to spread that new knowledge so that everyone across the organization can learn. The fourth capability is how to develop the first three capabilities of “See, Solve and Share” within the organization.
“See”
We don’t always see the details in any situation, and “that bias is a problem when it comes to being able to see and solve problems.” Thus, it’s important to be able to develop the skill of seeing, so everyone can see the problems, harm and the risks of harm. Meghan shared 10 hazards:
“The one that I think has the most potential in terms of being aware of hazards is motion, and wasted motion. I think you would be hard-pressed to think of a safety or harm event that occurs without some sort of motion involved. So thinking about how we move and interact with our environments, and the processes that dictate how we move is a huge potential and a huge opportunity to develop this crucial capability of being able to see where risks are, where hazards for harm potential can occur.”
Hazard recognition is a critical skillset to develop, as is “stop work” authorization. This is the express power to stop a process or activity where there is a risk of harm, or someone does not feel safe to continue.
“Solve”
A critical element in thinking about safety is that “every harm event will be solved to root cause and will be learned from.” The speed at which a harm event is investigated is essential to capturing information, context and observations while fresh in the minds of those involved. This real-time problem solving process is crucial to solving problems to root.
“If we truly want to get to root cause, and by root cause, I mean, what can we learn about what was at the root of this problem, and then be able to solve it or address that root cause to ensure that we never experience this problem again for that same reason. And not just by the person who experienced it, but for anyone in the organization.
Speed is key, and so leaders being able to show up when harm events occur, to facilitate and coach through that problem solving so you can understand exactly what led up to that event, is critical to real-time problem solving…. The organizations that do this best and engage all leaders in these capabilities should expect to reduce harm events by 50% year over year.”
“Share”
“It’s this idea of, how do we know, and how do we learn from each other what we can do in prevention after there has been an event.” Meghan then described three levels of sharing.
First is sharing the incident in the immediate area, so those in that area can take immediate countermeasures to prevent a recurrence, and begin to gather information. A second level is to share within the particular service line or site. This is important because there might be a similar hazard in another area where harm could be prevented by learning about it as quickly as possible. The third level is to share the incident, root cause, and countermeasures across the enterprise.
Meghan acknowledged that talking about sharing this way is easier to talk about than to execute. She offered the idea of a transparent real-time data-sharing system. This is essential to learning from all things gone wrong and building a true safety culture. “How are we engaging the rest of the organization in seeking out and looking for risks or harm that has been experienced in other areas so that we can learn from them ourselves.
"The organizations that do this best really focus on a transparent data system, where everyone can access real-time information, so that everyone, everywhere, every day also has a responsibility to put information in and to pull information out of, with the spirit of ‘we will get better every day, we will be safe every day.’”
“Coach”
This focuses on developing leaders as coaches, to develop the skills and learning of others to become problem solvers. “This might require a little bit of a different focus for leaders, for them to show up as coaches and not as the ones showing up to solve the problems themselves….
Establishing professional safety is key in this instance as well. Everyone must feel that they are respected and that their voice is important, and that their experience and lens through which they see the work is important in being able to solve problems.
Engaging everyone every day in solving problems is also key in this. Again, the experts in the work are the people who do the work, so their voice and their ability to solve problems will only accelerate your organization’s ability to sustain long-term change.
"It’s important to think about ‘coach’ as opposed to ‘implement.’ if I am improving on your behalf, while that might make me feel good and it might get us some short-term gains, it is me fishing for you. And the real way that the organization will accelerate and see transformational improvement that can be sustained long term is going to be by everyone’s ability to be able to get better."
“So engaging everyone every day, in the role I play as a coach is an important thing to think about and develop within your organization.”
“Change is there. Generational success is possible. Zero is possible. With the right engagement and leadership strategy, with the right focus and capability development of all of your people to see, solve, share, and coach people to be able to see, solve and share, with leadership, all things are possible.”
Meghan then answered questions from webinar participants, with questions ranging from leaders who care only about results, to A3s as a tool for use of real-time problem solving, to becoming more proactive by engaging in safety walks.
Watch the entire webinar to learn more about pursuing zero harm as a platform for embedding Lean capability.
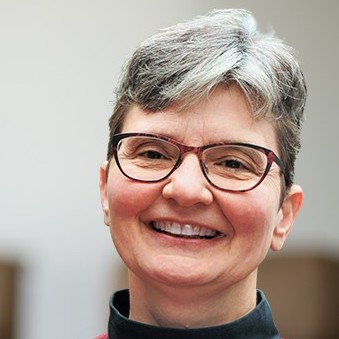
Written by Melissa Moore
Ms. Moore’s responsibilities center on marketing and communications. Prior to joining Value Capture, she served as a Marketing Manager at Reed Smith, a global law firm. Other career steps include: co-founding and operating a trend-setting coffeehouse; securities lawyer; and, service and equipment sales.
Submit a comment